The video above gives a broad overview of how The Micrex Process works. For a more technical representation of the development, see one of our early patents.
Configurations:
The Micrex/Microcreper has five base configurations: Comb Roll, Rigid Retarder, Bladeless, Flat Blade and Two Roll. In addition, five advanced configurations are available in-plant to our contract converting customers.
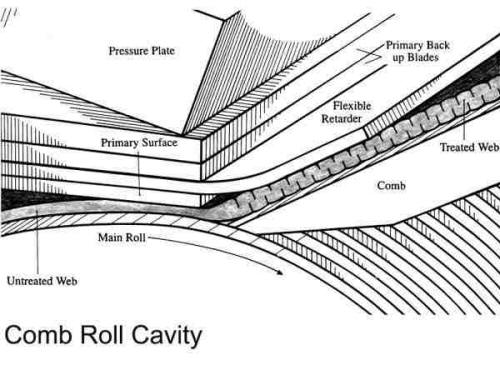
The Comb Roll configuration is widely used to soften hydro-entangled nonwovens and to crepe high basis weight substrates.
The Rigid Retarder configuration (the original Micrex configuration) can soften wet laid products and crepe paper, as well as process a wide range of nonwovens.
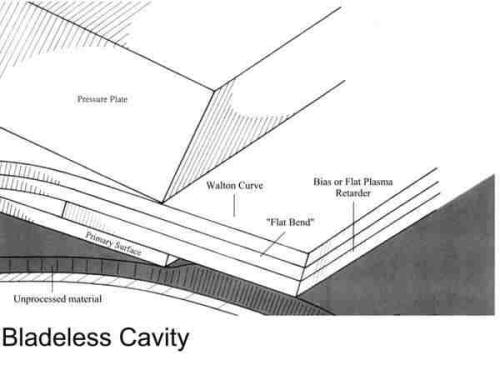
The Micrex/Microcreper equipped with a Flat Blade cavity is designed to give the textile finisher maximum flexibility to respond to a competitive style-driven marketplace.
A poly/cotton material can be made into a whole series of rich decorative styles. Many decorative styles are possible; plisse, crepe, and seersucker can all be created on the same basic material within minutes.
The process utilizes a specially formed blade, which selectively compacts the fabric. New styles can be configured by the operator using scissors, simply by cutting patterns in a steel blade. The spacing is limitless and is solely up to the finisher. The Micrex/Microcreper is able to impart a myriad of patterns with a relatively short changeover time, typically 2-3 minutes. In one case of a shower curtain manufacturer, the customer specified a 5 inch wide “pucker” with a 1/4 inch compacted width.
The Two Roll cavity — utilizing two drive rolls and two retarding blades, is at the core of the Micrex/Mark II technology.
Designed to minimize damaging heat at high speed, this system processes low melting point substrates such as polypropylene or polyethylene.
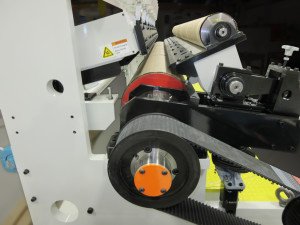
Representative Description of the Rigid Retarder Configuration